BALANCING LUXURY, SUSTAINABILITY AND COST
It served many other purposes throughout its history, but none as illustrious as housing the 124-room Hewing Hotel. The hotel’s name is a nod to the lumber industry that once propelled the city to its current stature.
TRANSFORMING HISTORY
The Hewing Hotel is one in a modest collection of not-so-modest boutique hotels curated by Aparium, a hospitality group specialized in the conversion of historic structures into upscale accommodations.
The hotel’s ambiance certainly fits the progressive, industrial chic vibe of the North Loop, thanks to ESG Architecture and Design and the work conducted by general contractor Greiner Construction. From the beginning, developers insisted that the facility perform – environmentally and fiscally – as well as it looks and feels.
The hospitality industry is known for its fierce competitiveness. High among a hotel’s opportunities to reduce costs is careful scrutiny of the systems that serve it. Heating, cooling, and DHW production represent about 60 percent of the energy consumed at a hotel.
ELIMINATING THE OPTIONS
“Minneapolis is a town of temperature extremes,” said Tom Suek, director of facilities at Hewing Hotel. “The comfort of hotel guests can’t be approached in an offhanded manner.”
Before the $38 Million renovation began, careful consideration was given to the heating and cooling system that would serve the hotel. Reducing energy use is certainly prudent, but environmental goals needed to be carefully balanced against the responsiveness of the HVAC system specified.
Being “green” also attracts guests, especially the affluent type. The looming question for the developers was whether or not minimizing the building’s carbon footprint was counterproductive to providing premium comfort while limiting upfront costs. This is especially true in a 126-year-old, 116,000-square-foot structure.
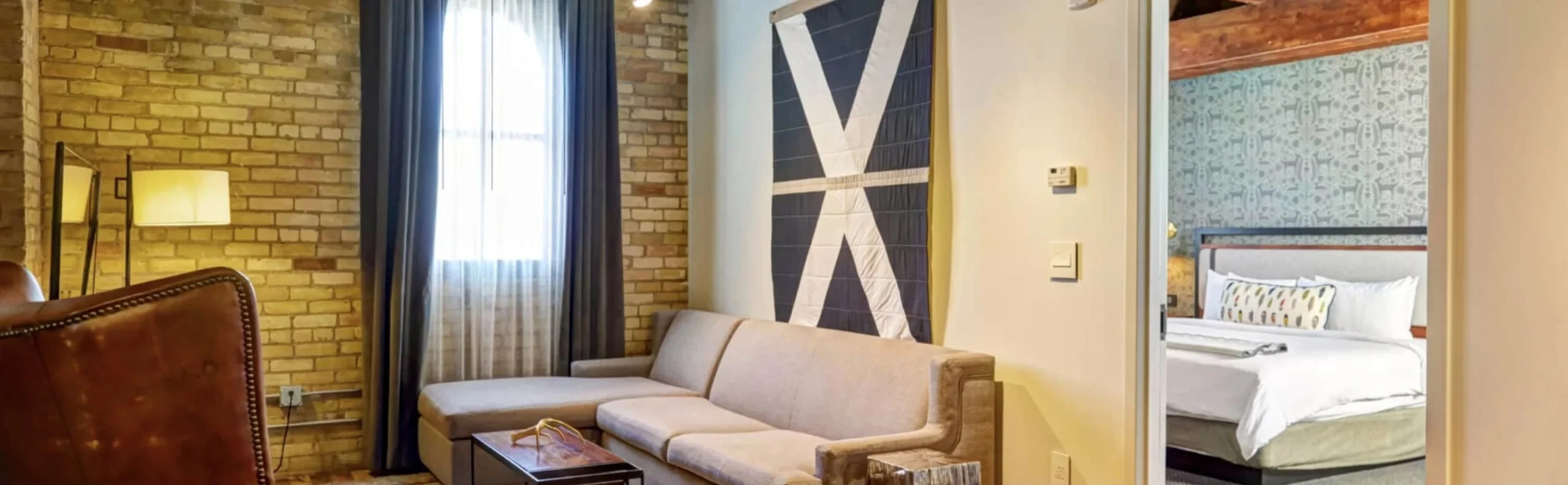
CHOOSING EFFICIENCY WITH IPS FAN COIL SYSTEM
In consulting with the developer on HVAC system selection, Kelly Hauenstein, sales engineer at Schwab Vollhaber Lubratt, Inc., explored numerous options for the Hewing Hotel’s HVAC system, including water source heat pumps, two- and four-pipe hydronic systems, PTAC units, VRF heat pumps, and IPS (integrated piping system).
PTAC units, while offering the lowest initial cost, were dismissed quickly because of their inefficiency, noise, and visual detraction from the interior space. Two-pipe hydronic systems, while efficient and long-lived, lacked the ability to heat one zone while simultaneously cooling another.
Water-source heat pumps and four-pipe hydronic systems were strong contenders due to their inherent efficiency and comfort, but were ultimately eliminated due to high upfront costs. VRF systems offered a middle-of-the-road alternative for initial cost, but lacked the system lifecycle that hotel management was seeking. The efficiency of VRF heat pumps in a northern climate also came into question.
“The customer kept coming back to the IPS fan coil system made by Williams Comfort Products,” said Hauenstein. “It had the right price tag, and it offered system longevity and the ability to simultaneously heat and cool adjacent zones without placing noisy equipment in the guest room. The fact that an IPS system would reduce the hotel’s use of refrigerants was icing on the cake.
DOUBLE DUTY PIPING
IPS is a piping system that utilizes the domestic water piping for hot and chilled water delivery to proprietary, NSF 61-certified fan coil terminal units. The same hot and cold water used to supply sinks and showers is also used in the system’s fan coil units. This can be achieved because there are two, constantly-circulating water lines throughout the building: one hot and one cold. Every component within the piping system is rated for potable use. The fan coil units are built with NSF/ANSI 61 & 372 certified copper. Each component within the fan coils and within the system, such as stainless steel circulators, is NSF-61 approved.
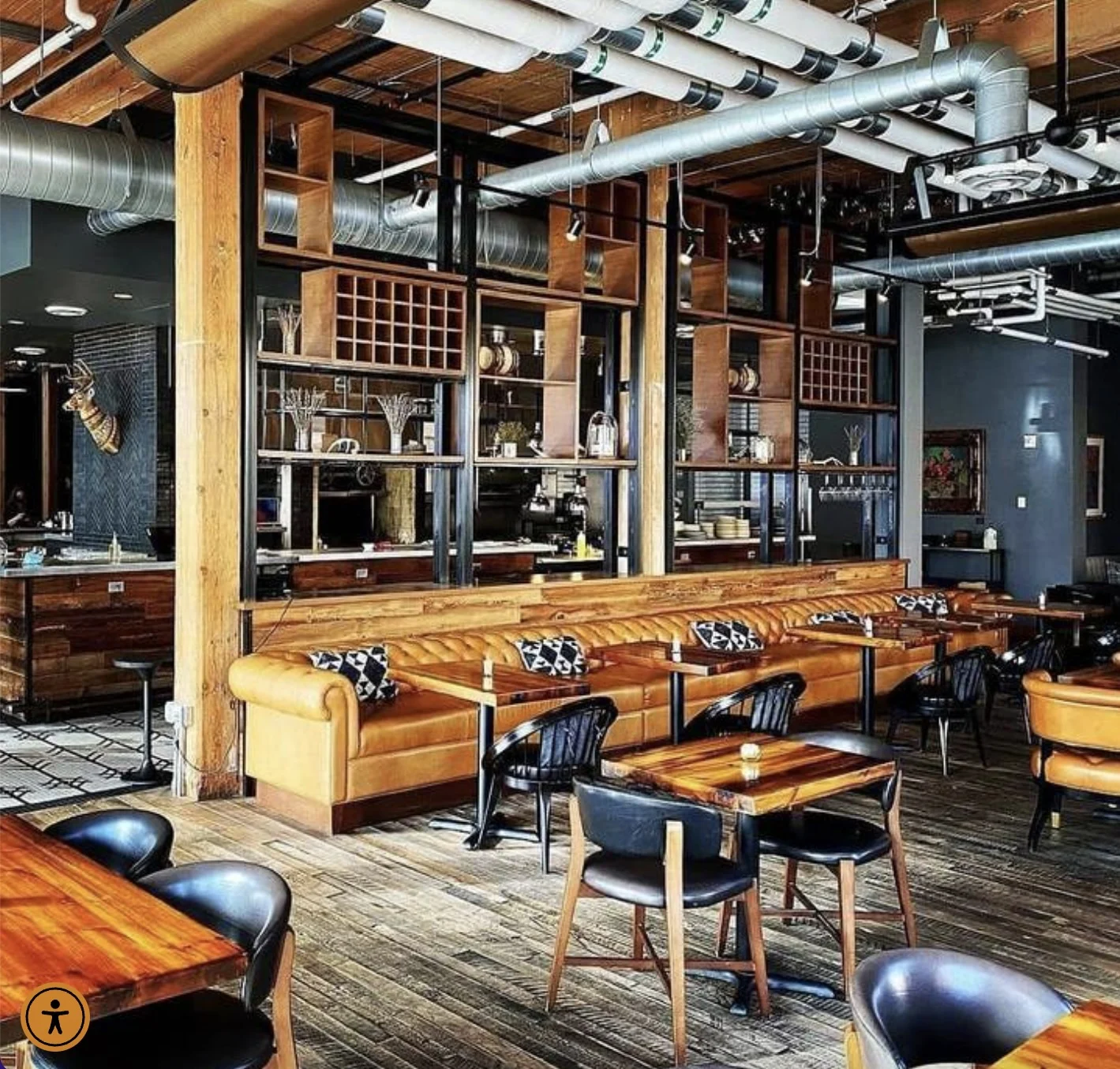
THE INNOVATIVE IPS SYSTEM
Total Comfort Solution pioneered the IPS system and has perfected the IPS fan coil design. Over the past decade and a half, IPS systems have been installed in hundreds of buildings throughout the US and Canada.
Using the domestic piping system to carry water for the HVAC system dramatically reduces installation cost and time. Because hot and cold water are available everywhere in the building at all times, IPS systems provide simultaneous heating and cooling in adjacent zones, just like a conventional four-pipe fan coil system. The savings is realized by eliminating dedicated hydronic system piping from the scope of work.
Hot water from the DHW recirculation line is introduced to the fan coil unit via a zone valve when the room’s thermostat calls for heat. After passing through the heating coil, it’s returned to the DHW line.
The system’s cooling function works in similar fashion. After passing through the fan coil unit, the cool water is returned to the chilled water line. The only unique element of the building’s cold potable water system is the presence of a return line.
In the event that there’s no call for heat or cooling for an extended period of time, Williams’ exclusive control board features a coil purge timer in each fan coil unit. Per ANSI standard, the control opens the coil’s zone valve for a brief period each day to eliminate the possibility of stagnation within the system.
The end result is a quiet, LEED-friendly heating and cooling system that provides significant savings on installation, maintenance, and operating costs for high-quality comfort. IPS installations are ideal for hospitality, assisted living, condos, apartments, or any other facility that’s occupied around the clock. In essence, IPS offers the efficiency and energy savings of a green system, but the affordability of a low-tech solution without placing noisy, maintenance-heavy components within the occupied space. “In addition to its other benefits, IPS offers the unique ability to capitalize on economizer cooling,” said Hauenstein.
ECONOMIZER COOLING
Because the domestic water in an IPS system serves double duty, the cold utility supply water can provide un-aided cooling so long as the water coming from the street is cool enough. This is called economizer cooling. In the case of the Hewing Hotel, utility water enters the building at an annual average temperature of 49°F.
During late summer, when utility water may be too warm to completely satisfy the cooling demand, a chiller is typically used to supplement cooling capacity for the cold water recirculation loop. To ensure safety of the potable water, the chiller is isolated from the domestic water via a dual-wall heat exchanger.
To further increase system efficiency, the cold water return line is used as a source of makeup water for the hot water system. After being used to satisfy various cooling loads throughout the building, the cold water return is warmer than utility water coming in from the street.